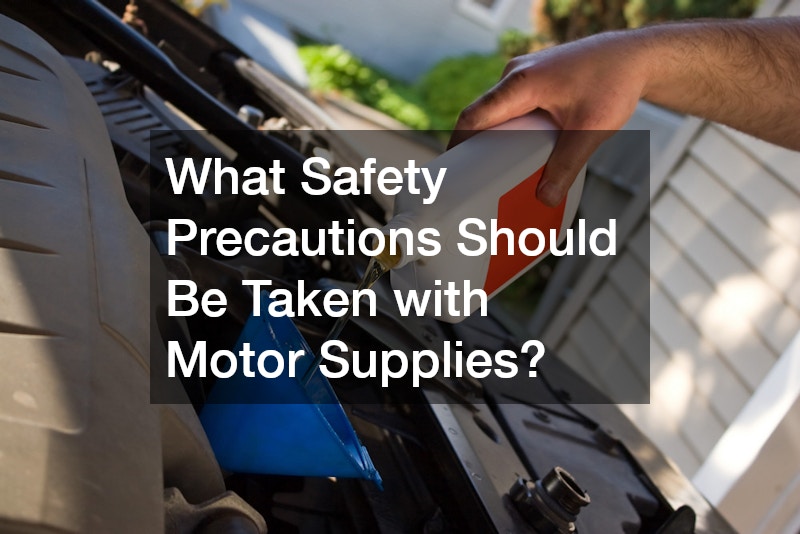
Importance of General Motor Knowledge
Motor supplies are an essential aspect of maintaining and operating various types of vehicles and machinery, but they also come with inherent risks. Understanding and implementing proper safety precautions when handling motor supplies is crucial to prevent accidents, injuries, and damage to equipment. Whether you are managing an auto shop, working in a repair facility, or maintaining personal equipment, following safety protocols ensures that operations run smoothly while minimizing potential hazards. From basic handling procedures to emergency response plans, every aspect of motor supply safety must be considered to create a secure environment for workers and equipment alike.
Understanding the Importance of Safety with Motor Supplies
The safety associated with motor supplies is often underestimated, but it plays a critical role in preventing accidents and equipment failure. When working with motor supplies, particularly in environments where electric motor service is involved, the risk of electrical shocks, short circuits, and fire hazards increases significantly. Being mindful of these dangers and taking necessary precautions can drastically reduce the chances of mishaps. The right protective measures, such as understanding the power ratings and the limitations of each motor component, help create a safer work environment. For example, ensuring that all motor supplies are correctly labeled and stored prevents confusion during maintenance, leading to fewer accidents and malfunctions.
In the specific context of electric motor service, extra precautions must be taken when dealing with high-voltage components. Electric motors often require careful calibration and routine inspection to prevent overheating or electrical surges, which can lead to damage or fires. Technicians must also wear appropriate personal protective equipment (PPE) when servicing these motors and ensure the power is completely shut off before beginning any work. Failing to do so can result in severe electrical injuries.
Proper Handling Procedures for Motor Supplies
The way motor supplies are handled significantly impacts both the safety and the longevity of the equipment. Proper handling involves adhering to established procedures to reduce the risk of personal injury and equipment failure. For example, basic safety protocols when handling motor supplies include ensuring that all workers are adequately trained in the correct methods of lifting, transporting, and storing heavy components, especially hazardous materials. Regular safety audits should be conducted to identify potential risks in handling procedures, and all team members should be kept informed of updates to safety guidelines.
When it comes to specific motor supplies, such as those used in car battery replacement, careful handling is crucial. Car batteries contain hazardous materials like acid and lead, which can cause severe injuries if mishandled. Proper handling procedures for car battery replacement include wearing protective gloves, using specialized tools for removal and installation, and ensuring that batteries are stored upright in a cool, dry place to prevent leaks or corrosion. Additionally, care should be taken to avoid short-circuiting during the replacement process, as this can lead to electrical shocks or damage to the vehicle’s electrical system.
Ensuring Correct Storage for Motor Supplies
Proper storage of motor supplies is an often overlooked yet vital aspect of maintaining safety in any automotive setting. When motor supplies are stored incorrectly, they can degrade faster or become hazardous, leading to potential accidents or equipment failures. In general, motor supplies should be stored in well-ventilated, temperature-controlled environments to prevent damage caused by moisture, heat, or cold. Items like oils, cleaning agents, and mechanical parts should be clearly labeled and placed in designated areas to avoid confusion or mishandling.
In the context of mobile auto detailing, correct storage becomes even more critical, as various chemicals and cleaning agents are used frequently. These materials often include solvents, waxes, and polishes, which can be flammable or harmful if not stored properly. For mobile auto detailing services, all motor supplies should be securely contained in leak-proof containers and kept away from direct sunlight or extreme temperatures. Additionally, any flammable liquids must be stored in certified safety cabinets to prevent fires.
Identifying Potential Hazards in Motor Supply Use
Identifying potential hazards when using motor supplies is a critical step in maintaining a safe environment. Every type of motor supply has its unique risks, and being aware of these can prevent accidents before they occur. General precautions include conducting regular risk assessments and safety inspections to identify faulty equipment or improper handling techniques. Workers should be trained to recognize the signs of wear and tear in motor supplies, such as frayed wires, leaks, or corrosion, which could lead to safety risks. By staying proactive in identifying potential hazards, workers can address issues before they escalate into dangerous situations.
In the specific case of auto window tinting, certain risks come with the chemicals and tools used in the process. For instance, the adhesives and cleaning agents employed can emit harmful fumes if used in poorly ventilated areas, posing respiratory hazards. Additionally, the tools used to apply tint films, such as razor blades and heat guns, can cause injuries if not handled correctly. To mitigate these hazards, professionals performing auto window tinting should work in well-ventilated spaces and wear protective gear, such as gloves and masks.
Implementing Personal Protective Equipment (PPE)
Personal protective equipment (PPE) is one of the most effective ways to safeguard workers when handling motor supplies. The general use of PPE, such as gloves, safety goggles, and protective clothing, can significantly reduce the risk of injury from chemicals, sharp objects, or electrical components. While some environments may require basic protective gear, others, especially those involving hazardous materials, might necessitate more advanced equipment, like respirators or flame-resistant clothing. Making PPE readily available and mandatory for all workers handling motor supplies is a simple yet effective strategy to ensure workplace safety.
In brake service, the need for PPE is particularly high due to the nature of the supplies and tools involved. Brake dust, a byproduct of worn-out brake pads, contains particles that can be harmful if inhaled. Therefore, wearing respirators and protective eyewear during brake service is crucial to prevent respiratory and eye damage. Additionally, gloves should be worn to protect against sharp tools and chemicals used to clean and lubricate brake components.
Safe Operation of Motor Equipment and Tools
The safe operation of motor equipment and tools is paramount in any automotive environment, as improper use can lead to serious injuries and equipment damage. General safety practices include thoroughly reading and following the manufacturer’s guidelines for each piece of equipment, conducting routine maintenance, and ensuring that all tools are in proper working condition before use. Motor supplies, including tools like wrenches, jacks, and power tools, must be used with care and precision. Workers should always be aware of their surroundings and avoid distractions when handling tools.
For auto mechanics, the safe use of motor supplies is even more critical, as they work with a wide range of tools and equipment daily. From hydraulic lifts to air compressors, each piece of equipment requires specific safety protocols. For instance, improperly using a lift can cause a vehicle to fall, leading to severe injury or damage. Mechanics must be trained to safely operate this equipment and understand how to inspect it for potential issues before every use.
Maintaining Equipment to Prevent Safety Risks
Regular maintenance of motor supplies is a crucial factor in preventing safety risks and prolonging the life of the equipment. General maintenance tasks include cleaning tools after each use, performing regular inspections for wear and tear, and replacing any defective components before they cause failures. A proactive approach to equipment maintenance not only ensures smooth operations but also minimizes the risk of injuries caused by malfunctioning supplies. By scheduling regular maintenance checks and creating detailed records of equipment conditions, automotive businesses can ensure that their motor supplies remain in good working order and reduce the potential for accidents.
In tire repair, maintaining equipment is particularly essential, as worn-out or malfunctioning tools can compromise both safety and service quality. For example, tire repair equipment, such as pneumatic tools or tire balancers, must be regularly inspected for issues like air leaks, worn hoses, or misalignment. Failure to maintain these tools could result in serious accidents or improper repairs, leading to unsafe driving conditions for customers.
Training Employees on Motor Supply Safety Protocols
Proper training on motor supply safety protocols is essential for ensuring that all employees understand the risks associated with the supplies they handle and how to mitigate them. General safety training should cover topics such as the correct use of motor supplies, emergency response procedures, and the identification of potential hazards. Regular refresher courses and hands-on training sessions help reinforce safety practices and ensure that all team members remain updated on the latest safety standards. By cultivating a culture of safety through thorough training, companies can reduce workplace accidents and ensure that all employees are equipped to handle motor supplies responsibly.
In an auto glass repair company, safety training is especially important due to the specialized tools and materials used. Employees must be trained to handle glass safely, prevent cuts and other injuries, and must understand the proper techniques for removing and installing windshields. Additionally, the adhesives and chemicals used in auto glass repair can pose respiratory risks if not used in a well-ventilated area, making PPE and proper ventilation key topics in any training program.
Emergency Procedures for Motor Supply Incidents
Accidents can occur even in the safest environments, making it essential to have clear emergency procedures in place when working with motor supplies. General emergency protocols should include steps for responding to fires, chemical spills, electrical malfunctions, and personal injuries. All employees should be familiar with evacuation routes, the locations of fire extinguishers, and first aid kits. In addition, a well-communicated chain of command should be established for emergencies, ensuring that employees know who to report to and how to take swift action in case of an incident. Regular emergency drills help keep everyone prepared for potential motor supply-related emergencies.
In the context of windshield replacement, specific emergency procedures must be in place due to the risks associated with handling glass and adhesives. If a large glass pane shatters during installation, employees must know how to safely clean up broken glass to prevent cuts and further accidents. Similarly, adhesive spills can create slipping hazards, which should be addressed immediately to avoid falls. In both cases, having appropriate emergency procedures in place ensures that incidents are managed quickly and efficiently, minimizing injuries and downtime.
Complying with Regulations for Motor Supply Safety
Adhering to industry regulations and standards is an integral part of ensuring safety when working with motor supplies. Regulations vary depending on the type of motor supplies and equipment in use, but they often include requirements related to equipment maintenance, personal protective equipment, chemical handling, and waste disposal. Compliance with these regulations helps prevent accidents and avoids costly fines or legal issues. Automotive businesses need to stay up-to-date on any changes in safety regulations, conducting regular audits to ensure all procedures and equipment meet the required standards.
For car AC repair, compliance with safety regulations is particularly important due to the use of refrigerants and other chemicals that can be harmful if improperly handled. Regulations require that technicians use specific tools to safely capture and store refrigerants to prevent leaks that could harm the environment and pose health risks. Additionally, proper disposal of hazardous materials must be followed to ensure the safety of both the workplace and the surrounding environment.
Implementing Motor Parts Knowledge
Motor supplies are a crucial part of any automotive operation, but they come with inherent risks that must be managed carefully. By implementing robust safety protocols and ensuring that all employees are trained in the proper handling, storage, and use of these supplies, businesses can minimize the risk of accidents and maintain a safe working environment. From understanding the importance of motor supply safety to complying with industry regulations, every step in the process plays a vital role in protecting both workers and equipment. Whether performing tasks like electric motor service or windshield replacement, taking the time to assess hazards, maintain equipment, and follow safety guidelines will ensure the smooth operation of automotive services. In doing so, businesses not only protect their employees but also uphold the integrity and longevity of their motor supplies, contributing to a safer, more efficient work environment.